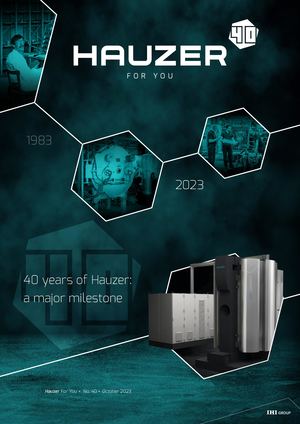
HAUZER FOR YOU #40
by IHIHauzer
HAUZER FOR YOU #40
FO R YOU 1983 2023 40 years of Hauzer: a major milestone Hauzer For You No. 40 October 2023
Dornbracht: Elevating design with unparalleled finishes 28 A successful anniversary celebration 06 16 08 32 2 Hauzer for You No. 40
Content 04 Introduction Dave Doerwald 06 A successful anniversary celebration 08 Millenia Technologies 10 Ionbond India 12 A Hauzer history 16 Hauzer Flexicoat® 500 ready to order 18 One-stop shop at Hauzer USA 21 Hauzer Flexicoat® 1500 R&D system 24 Energy-saving upgrades 26 CVI coating technology update 28 Customer story: Dornbracht 30 Plasma cleaning, etching and nitriding 32 Customer story: Albrecht + Schumacher 34 Developments in the hydrogen economy 36 Permanent Helpdesk support 38 HR updates 42 New Bernex website Publisher: IHI Hauzer Techno Coating B.V. 5902 RB Venlo The Netherlands T +31 77 355 97 77 info@hauzer.nl hauzertechnocoating.com Editor: Daisy Ripmeester Writer: Maartje Gorte Design: Bluehub.nl No responsibility can be accepted for the correctness or completeness of the statements made, especially in the case of external contributions. The opinions expressed in this magazine do not necessarily reflect those of IHI Hauzer Techno Coating B.V. We reserve the right to make technical changes. Reprinting or reproduction of any kind is prohibited. Exceptions to this rule are possible only with the prior written permission of the publisher. Disclaimer ®: Registered Trademark in EU and selected countries only © IHI Hauzer Techno Coating B.V., all rights reserved. 3
Here’s to the next 40 years, together Welcome to our special anniversary edition of the Hauzer for You! We are proud of 40 years of challenge, development and success, and we are happy to share some of our historical milestones with you. Our celebratory dinner and conference were a big success as well, and we heard many good things from our team and the people attending. Championing the role of coatings in sustainability Sustainability is an important topic in many markets, which is why we devoted our Celebratory Conference to the topic with speakers from academia and industry. Coatings will be a very important enabler of many more sustainable technologies, and we hope that our systems and technologies will play an important role in the transition toward a zero-carbon world. In this Hauzer for You, too, we spend time on the topic with an update from our H2 Product Team and interesting energy-saving upgrades for Hauzer and Bernex systems. Celebrating developments, customers and partners worldwide Hauzer has only been able to reach our level of success over the past 40 years thanks to our customers, partners and suppliers. In this edition, we talk to two recent additions to the Hauzer family: Albrecht + Schumacher and Dornbracht. We also have two articles on the opportunities in the Indian market, one from our customer Ionbond India and one from joint Hauzer and Bernex agent Millenia. For our customers in decorative markets, we’re happy to introduce our new Flexicoat 1500 R&D machine, which will allow us to develop coatings at scale and more easily industrialise them. We hope you will enjoy these articles and more – including the introduction of the new Bernex General Manager, Olivier Coddet. We are very happy to have him on board! 4 Hauzer for You No. 40
5
Looking back on a successful anniversary celebration 40 years ago, Hauzer Techno Coating was founded. Today, we are a leading provider of physical vapour deposition (PVD) equipment, setting the quality standard worldwide for our modular systems, proven technology and great long-term partnerships. That is worth a celebration! From 12-16 June, Venlo was the scene of the ever-wonderful HIPIMS Conference, the Hauzer Celebratory Dinner and the Hauzer Conference. “I am very happy about how our anniversary celebration turned out,” said Dave Doerwald, Hauzer CEO. “I’ve only heard good things about it from everyone who visited – our long-standing partners, old and new customers and of course our suppliers. It was wonderful to see so many in one place. It is thanks to everyone we worked with over the years that Hauzer has been able to become what it is today, and we hope to celebrate many more future milestones together.” Hosting the 13th HIPIMS Conference in Venlo The HIPIMS Conference has been a leading gathering of experts and users of HiPIMS technology since 2010. It’s organised annually by Sheffield Hallam University and the Fraunhofer Institute, both highly A delightful walking dinner against the esteemed institutes in the field of thin-film coating. Venlo skyline It was an honour for Hauzer to be able to host the On the evening of Thursday 15 June, Hauzer’s VIP 13th edition of the conference here in our hometown guests gathered on the top floor of the Van der Valk of Venlo. This marks the long-standing relationship Hotel for a lovely sunset dinner, accompanied by a between Hauzer and SHU, ever since former Hauzer jazz trio. The participants included long-term and General Manager Dieter Münz established the Chair new Hauzer customers, and our valued research of Surface Engineering at SHU in 1993. and collaboration partners, suppliers and global distributors. During the evening, people enjoyed several courses of creative dishes, drinks and lively conversation. Jointly building a future to look forward to On Friday, everyone gathered bright and early for a morning full of energising talks on future technology, sustainability and industry optimization by leaders from industry and academia. Dave: “Sustainability is a topic on everyone’s agendas. That is why we gave it pride of place at our Hauzer Conference. Hydrogen technology, in particular, is very interesting to Hauzer – it will require cutting-edge new coatings and the most optimum production processes to meet the market needs for fuel cells in the future. We hope to 6 Hauzer for You No. 40
Finishing the day off with Hauzer, at Hauzer Stephane Cotte, Manager of the Materials Engineering Then it was time for the Hauzer factory tour. Visitors division of Toyota Brussels viewed all the Hauzer machines currently being built, Toyota focuses on becoming more sustainable as the analysis lab, and the Hauzer R&D machines – a company, in the face of climate change as reality. including the fully functional Flexliner. There were Their Environmental Challenge 2050 strives for zero opportunities to ask in-depth questions and view CO2 emissions from plants, vehicles and even the car’s some recent breakthroughs in decorative colour entire life cycle. So far, Toyota sold 20+ million hybrid samples. The star of the show was a Toyota Mirai fuel vehicles since the launch of the first, groundbreaking, cell electric vehicle, generously on loan from Toyota Toyota Prius in 1995. Oostendorp in Helmond, giving us a taste of what the future of mobility looks like. Richard van de Sanden, director of the Eindhoven Institute for Renewable Energy Systems (EIRES) at Conference speakers and highlights Eindhoven University of Technology Hiroshi Nakai, Technical Advisor IHI Van de Sanden has one motto for sustainable The main goal of IHI is to create a world where nature solutions: that their future is not in size, but in and technology work in unity. As part of the IHI number. Historically, smaller units evolve faster than Group, Hauzer’s coating equipment is expected to bigger ones, which is in part why the cost of solar play a clear and critical role in achieving that. energy has dropped by several orders of magnitude in the last few decades, while the cost of nuclear Christoph Hermann, Director of the Institute for power has held more or less steady. In the coming Surface Technology at the Fraunhofer Institute years, the market for small-size solutions to storing Industry can increase its sustainability through better intermittent surplus power will change the face of planning and control, and by focusing on energy. industry in Europe. Automatic climate control in dry rooms can reduce energy use by 30%, for instance. The focus on energy also changes how recycling is viewed: it is often not the loss of material that is the most wasteful, but the use of energy to get the material to the right form for use in industry. The main point: life cycle thinking is critical to solve these sustainability challenges. 7
Millenia Technologies: expert agent in India India, rapidly growing as one of the top global economies, presents an exciting market for technological advancement and innovation. Since 2018, Bernex has worked with Millenia Technologies, a specialised agent, to provide companies in India with access to Bernex CVD systems, training and support. More recently, Millenia also became the dedicated Indian agent for Hauzer. Together, the three companies are committed to advancing the coating industry in India. 8 Hauzer for You No. 40
Supporting the manufacturing industry in India “Millenia Technologies is a versatile player representing various international precision cleaning, coating, measuring and finishing equipment companies,” explains Gautam Tiwari. With 25 years of experience, Gautam leads the Millenia Technologies team in a wide range of industries, including automotive, jewellery, cutting tools, aerospace and medical. Gautam: “The technical line-up of companies we represent provide tremendous synergy in these markets, and Millenia is excellently positioned to help our customers raise their manufacturing to a higher level.” With the addition of Hauzer to the portfolio, Millenia now represents both physical and chemical vapour deposition technologies, covering a broader spectrum of state-of-the- art coating technologies for India’s growing industry. Full partner for sales, support, spare parts and consumables Millenia offers more than distribution. They also have a robust technical support team, trained at the Hauzer and Bernex competence centres. This technical support team has high-level expertise: they can install and upgrade machines by themselves, with only remote support from Bernex and Hauzer. Although this was first tried as a necessity during the Covid pandemic, this proves that the team has the required technical skill to offer excellent customer support for any Hauzer and Bernex customers in India. Millenia’s 45-strong team, including several tech support specialists trained in Switzerland and Venlo, provides comprehensive solutions. Gautam: “From selling the product to supporting installation, training, and even direct marketing, we’re a long-term partner ensuring a seamless customer experience.” Expanding reach in India India’s growth is propelled by a shift in technology and entrepreneurship, and the country is set to become a significant supplier to the world in the near future. Bernex and Hauzer, through their association with Millenia, want to tap into this potential in various new sectors, such as the textile industry. So far, Millenia’s customers for CVD and PVD equipment are mostly internationally active companies with manufacturing plants in India. They already have experience with Bernex and Hauzer coating systems from their plants in other countries, and they highly appreciate the Hauzer Group’s global reach and support organisation. But with the growth of the Indian middle class and with international companies active in India, there is a tremendous opportunity for high-quality products made by Indian companies as well. Although cost remains a crucial factor, Indian companies are investigating more high-tech equipment for future investment. “For now, companies are perhaps buying less customizable PVD and CVD coating equipment,” says Gautam. “But we see that they are taking note of the superior quality of Bernex and Hauzer machines.” 9
10 Hauzer for You No. 40
Ionbond India: innovating coating technology for an expanding market As part of the IHI Group, Ionbond is a well-known user of Hauzer equipment, with global reach. In India, Ionbond has two facilities at Pune and Chennai. From these locations, Ionbond India focuses on providing physical vapour deposition (PVD) and plasma-assisted chemical vapour deposition (PACVD) coatings for cutting tools, forming and moulding tools, automotive and industrial components, and more. For this edition of Hauzer for You, we interviewed Atul Kulkarni, Executive Director of Ionbond India to hear more about their expertise. A proud legacy of coating facilities in India In addition to the broad portfolio of standard coatings, customers “The two locations in India have a long history,” says Atul. “The can also contact Ionbond India for tuned or customised coatings. plant in Chennai was started way back in 1992 and the one in Pune The local engineering teams and colleagues from the Dutch and in 1994. We’ve been part of the global Ionbond network since French Ionbond competence centers work together to serve 2005.” From these locations, both coating centers offer speedy customer needs. “We have a focused consistent drive,” says Atul. deliveries to PAN India customers to fulfill their requirements. “Providing fast, consistent and high-quality coatings so that our “Our main motto is to deliver reliable high-performance coatings customers can achieve their goals.” to customers and productivity to stakeholders,” Atul adds. “Since we joined Ionbond, we have seized more techno-commercial Interesting opportunities in the Indian market opportunities by investment in state-of-the-art technology and The Indian market is expanding and bursting with opportunities. machinery. This has supported us in creating deeper connections “Many international companies have started their joint ventures with our esteemed customers.” or own manufacturing in India, or added to existing ones,” Atul observes. “The next decade will be a turnaround for India. Reliability with Hauzer systems The rapid industrial growth, boost in automotive electrification, When it comes to machine reliability and coating quality, Ionbond rise of India’s vast local market – all these are going to provide India trusts Hauzer equipment for its uptime and consistency. massive opportunities.” “These machines have positioned us ahead of our competitors,” notes Atul. Ionbond India offers a diverse coating portfolio In addition to this, the medical sector is especially promising tailored to different market segments. “With our Hauzer Flexicoat in India. The expertise in Indigenous Vedic as well as Western 1200, we are offering all the Ionbond Tetrabond coatings. Medicine is serving both Indian and foreign citizens. “We aim to Our Hauzer Flexicoat 850 model allows us to offer the unique focus on medical coatings and are looking for more support from range of the Plus coatings as well. The Indian market has shown Hauzer in terms of technologies and capacity,” says Atul. “On the strong confidence in these coatings.” whole, we’re gearing up for expansion. We are confident that we can operationalise any new coating technology and machines to its capacity in a very short time.” 11
A Hauzer history: 40 years of milestones 1983 Hauzer Techno Coating founded by the Hauzer family. 1980 1982 1984 1989 1987 1988 1986 First machine for the tool coating market (arc evaporation technology). HVM Plasma Fraunhofer IST HVM Plasma has developed and supplied core components Hauzer’s success is also based on long-term partnerships with for Hauzer equipment since the early 90s. Michiel Eerden, academia. For instance, with the Fraunhofer Institute for Surface Director of Sales: “The quality of the HVM products we use Engineering and Thin Films (IST), an internationally recognised in our machines, such as cathodes and tables, is crucial for partner for research and development. Christoph Herrman, achieving our quality goals.” Jiři Vyskočil, founder of HVM Director of Fraunhofer IST explains: “The history between the Plasma: “Hauzer and HVM have worked together for the past Fraunhofer Institute for Surface Engineering and Thin Films (IST) 33 years. We have a very good relationship, where we can goes back to the founding years of the institute, in the late 1990s, exchange ideas and knowledge. It’s like one big family.”peers when the first Hauzer machine was installed. but in all layers of the company.” 12 Hauzer for You No. 40
First machine for decorative 1996 applications – introduction of the HTC-1500 platform. 1998 1997 1995 1992 1993 1999 Massive 1991 growth of the decorative 1990 market for Hauzer. 1994 First machine for the tribological coating market. Werner Fleischner, Hauzer Director 1991-2001 “I was director of Hauzer in what I call the development phase. In the 90s, we also started coatings for automotive applications. At this time, we made only tool coatings. Soon, we expanded By the late 90s, we were the leading company in the world for to forming tools and accepted our first order for a decorative decorative coatings and automotive parts, thanks to the ability golden coating. The successful technological developments we of our systems to make complex and tailored PVD coatings. did for those markets opened even more doors. Needless to say, I am still very proud of what we achieved.” 13
A Hauzer history: 40 years of milestones 2008 IHI Group, Japan, becomes new owner of Hauzer Shinji Dairen, Hauzer Chairman of the board, General Manager of the Heat Treatment & Surface Engineering Business Unit in IHI Corporation. 2002 “In Hauzer, we saw a way to bring new approaches First mass production systems built for and options to the processing of base materials, DLC coatings (automotive) - introduction and to aggressively enter the global market. of the Flexicoat 1200 platform. This furthers IHI’s ambition to become a global leader in the growing markets of heat treatment and thin-film technology. IHI expects Hauzer to continue to be a global leader. They will keep providing solutions for customers, adding value 2003 and creating new functionality. Those services Hauzer becomes market leader for will contribute to decarbonization, a more coatings in automotive market. environmentally friendly, circular society, and healthy and secure living.” 2000 2002 2004 2006 2008 2010 2003 Opening of competence centre in Venlo, NL. 2011 Establishing the first Hauzer competence centre First HiPIMS system. was a major leap in R&D, analysis and assembly capability, allowing for further growth and collaboration with our partners and customers. 2010 Opening competence centre in Thomas Krug, Hauzer CEO 2004-2014 Shanghai, China. “Hauzer’s company culture is the foundation of our From Shanghai, we are able to serve our success. It’s always been a very open culture, feeling customers in China with support, spare like a family where people are allowed – and encouraged parts and training. This competence – to say what they think. And not just to their direct peers centre expanded Hauzer’s global reach but in all layers of the company.” and presence considerably, allowing us to focus more on our customers. Luis Sobral, Engineering Manager and Technical Global Coordinator for Piston Rings at MAHLE: “IN 2022, we needed a strong supplier with a reliable machine and the possibility to develop a new PVD coating for piston rings. Hauzer was rated the highest on reliability and productivity, exceeding our expectations at the time. The support of Hauzer engineers was crucial in winning the project. MAHLE and Hauzer have had a strong relationship ever since.”
2023 2022 The 1000th machine (PVD/CVD) delivered worldwide. Launch of Hauzer Together, Hauzer and Bernex have delivered over 1000 Flexliner® inline system. coating systems worldwide by now. This is an amazing milestone. With the Hauzer Flexliner® Perhaps even more amazing: the vast majority of these systems platform, we took our inline are still in use today, thanks to the modular, robust design of the coating expertise to the next equipment, and the upgrades developed by Hauzer and Bernex. level. Even better technology, engineering, flexibility, pro- ductivity and cost of ownership – all to provide the same Hauzer quality. 2023 Start of new H2 Product Team & installation of a Hauzer Flexliner in our competence centre in Venlo, for coatings for bipolar plates . Hydrogen technology is going to be pivotal in the transition towards carbon neutral 2022 manufacturing, living and transportation. Opening of Hauzer USA. Hauzer is planning to play an important Now, we can provide support to our role in getting fuel cell technology and customers in North America in their own time electrolysers to a point of affordability and zone, with service, training and spare parts. availability, and our team of experts will drive this pillar within Hauzer. 2022 2012 2014 2020 2016 2018 2011 Opening competence centre in Yokohama, Japan The new competence centre in 2019 IHI Bernex becomes independent CVD, Japan does for the rest of Asia and CVI, CVA supplier in the house of Hauzer. Oceania what the office in Shanghai By welcoming Bernex to the Hauzer Group, did for China. Hauzer always strives we offer a full portfolio of coatings. Bernex has to be close to customers, and that been setting the standard for chemical vapour includes geographically. deposition (CVD) coating technology and its variants for decades, and we are proud to work with them so closely. 2012 Launch of Hauzer’s first inline platform, the Metalliner. 2023 Hauzer turned 40! And of course we celebrated. Read all about our anniversary event on page 6. 2013 First CARC+ system.
Big milestone for the Hauzer Flexicoat 500 ® platform Last year, we introduced our new Hauzer Flexicoat® 500 physical vapour deposition (PVD) coating platform. With this smaller system, customers can enjoy the same high Hauzer quality. Today, we are proud to announce a big milestone: the first Flexicoat 500 machine is complete, and we are ready to start taking orders. Getting ready for the market “Assembly of our prototype is finished,” says Michiel Eerden, Director of Sales. “We’re excited to show the coating quality this machine can produce. Because the Flexicoat 500 is more standardised than our fully modular machines, it will have a significantly shorter build time. This is great for customers who would like to get started with Hauzer technology faster.” This first Flexicoat 500 machine has CARC+ technology installed. “This is one of the most important technologies for the tool sector,” says Michiel. “Now the prototype is complete, we will start adapting other technologies. The first on our agenda is sputtering.” Come see for yourself! The Flexicoat 500 has made its virtual reality debut at the EMO trade show. Would you like to see it in real life? Feel free to make an appointment at the Hauzer Competence Centre in Venlo. The Flexicoat 500 platform was developed with coating service providers, coating researchers and start-ups in mind. Take a look inside the Flexicoat 500 with our VR video: Are you interested in seeing what the Flexicoat 500 can do for you? Contact Michiel Eerden for more information at +31 77 355 97 04 or MEerden@hauzer.nl. 16
17
One-stop shop at Hauzer USA Since its opening in 2022, Hauzer USA has been growing steadily. As North American support organization for the two largest producers of physical and chemical vapour deposition (PVD and CVD) machines in the world, they offer global reach and experience, from a much more convenient location. Especially when it comes to spare parts delivery, Hauzer USA has much to offer: parts on the shelf, ready to ship out same day, and with no or very little delay at customs. Michael Martin, Business Manager Hauzer USA, says: “We now have field service engineers for both Hauzer and Bernex machines, plus an inventory and office specialist to manage the day-to-day operation of our growing office and warehouse. It has been a busy summer, between customer visits, trade shows and handling support requests!” Service modules, training, and more! Michael: “At Hauzer USA, we want to be a one-stop shop, your resource for everything you need for your Hauzer and Bernex machines. We have the capacity to provide sales, service and spare parts, all within your own time zone and within reasonable travel distances. In addition, we’re part of a company with global coverage, so from the Hauzer Group we offer full support worldwide. That’s a big benefit for multinational companies, companies focusing on onshoring, and companies working with international suppliers that need to meet certain quality standards.” Looking to get the most return on investment on your service agreements? Hauzer and Bernex both offer service modules, allowing you to choose the right service levels and types for your business plan. The training module in particular is very interesting for companies in the United States. “High turnover is standard in many industries,” says Michael, “and it is not always easy to have a succession plan in place. In addition, many highly specialized people are retiring, reducing the availability of skilled staff in all technology sectors. With the Hauzer and Bernex training modules, you can upskill your own staff. And of course, our other service modules save you the need to have trained service engineers on staff.” Next steps with Hauzer USA “The most important thing our customers in North America can do right now is to register Hauzer USA as a vendor in their systems,” says Michael. “That way, when you have a support need, we are all set to help you out in the least amount of time possible. We’re here, we have the parts, and we have the people.” Got any questions? Please contact Business Manager Michael Martin at +1 248 571 2689 or MMartin@hauzer.us. 18 Hauzer for You No. 40
Trends in the busy American market on next page 19
Trends in the busy North American markets Automotive The automotive industry in Canada, Mexico and the United States is going through some fast transitions. Everyone is aware of the ongoing shift from combustion engines to battery or fuel cell vehicles. Decorative In the decorative sector, protective PVD coatings in beautiful colours are increasingly popular for faucets, sinks, door hardware and premium luxury items such as watches, phones, and glasses. Hauzer is a world leader in these decorative coatings and is constantly developing new and trend- setting colours. “An important quality that luxury brands are looking for is fingerprint resistance,” says Michael. “This is also on the Hauzer agenda.” Antibacterial coatings The Covid pandemic has increased global interest in public health. Hauzer developed a decorative coating with antibacterial properties, for applications in hospitals or crowded public areas. Medical For medical applications, the Hauzer deposition technology portfolio has enticing possibilities for surgical instruments and medical implantable devices. Michael: “In our last round of company visits, we visited medical supply companies in the United States. They all know of Hauzer and are interested in our equipment.” Tool The tool industry is a long-time user of both Bernex and Hauzer equipment. “We’re particularly pleased to be able to service tool manufacturers and regrinders from their own time zone, with field service engineers specialized in PVD and CVD,” says Michael. “Madison Heights is a perfect location to support heavy industry both locally and further afield.” Turnkey solutions for everyone In addition to solutions for all these industries and more, both Bernex and Hauzer have the option to provide turnkey solutions. “Buying all your equipment from a single source means it is all guaranteed to work together – both in our factory and yours,” says Michael. “And for Hauzer USA as a service organisation, it means we can support our customers with these machines as well. That takes even more weight off their shoulders.” 20 Hauzer for You No. 40
New, state-of-the-art R&D system at Hauzer for decorative coatings Text will follow New, state-of-the-art R&D system at Hauzer for decorative coatings To serve our customers in an industry that thrives on innovation and technological finesse, Hauzer built a new R&D system that is an accurate reflection of the technologies our customers have in house. It houses all our technologies used for decorative coatings, on our largest Hauzer Flexicoat ® size – the 1500 Max. With this machine dedicated to coating development, we can help our customers in the decorative sector with new coatings, troubleshooting, scaling, and more. 21
Fully equipped with technology The new R&D system has all available Hauzer technologies that are relevant for decorative coating development: HiPIMS Magnetron sputtering Rectangular arc PACVD Plasma polymerisation Technology for improved coating homogeneity It can apply these technologies at the same time (for combined coatings) or sequentially (for multilayer coatings), and is ready to be upgraded with future technology as well. Daniel Barnholt is the process engineer who will be responsible Fully equipped with technology for managing the new R&D system. “One requirement for the The new R&D system has the latest options for optimising colour R&D system was that it can run all existing coatings and colours uniformity over the height of the coating chamber. The benefit in the decorative Hauzer portfolio,” says Daniel. “With the new of developing this for customers is that they can load more technologies and expertise, it will also help Hauzer engineers products per batch while still enjoying good, consistent colour. expand our portfolio in new directions. The Flexicoat 1500 Max That makes it possible to, for instance, assemble a bathroom tap R&D system is the largest machine available for development and with components coated at the top, middle and bottom of the sampling at Hauzer, and I’m looking forward to seeing all that we chamber without visible colour differences. can do with it.” Improved colour consistency over the height of the coating chamber. For all colour measurements in L* (black/white), a* (green-red) and b* (blue-yellow), the new technology results in a narrower bandwidth of colour ranges. This means that the resulting colour will also be much more uniform than before. 22 Hauzer for You No. 40
Developing your coatings directly to scale Still a productivity powerhouse Huub Vercoulen, Sales Manager, explains the rationale behind Being set up as a highly experimental development machine the new R&D system: “The Flexicoat 1500 and 1500 Max are by far does not reduce the Flexicoat 1500’s base productivity in the the most common systems we sell to customers working in the slightest. “It’s still the machine with the fastest cycle time,” says decorative sector. We wanted to invest in a development system Huub. “It can coat metal and plastic, and it can achieve all quality that is representative of the actual machines our customers requirements. We gave it the newest equipment and hardware have. That way, when we develop a new coating or help them for all technologies, even the standard ones. For instance, it troubleshoot their application, our engineers won’t have to go has a dedicated, brand-new dry pump; the arc power supply is through the process of scaling up. Developing coatings in the water-cooled; and so on. This machine has the best Hauzer can same size coating machine as the production system makes it offer in large batch machines today.” much easier to transport recipes, technologies and colours to our customers’ equipment.” Want to book testing time on the new R&D machine? Reach out! Ready for bold experimentation If you have any challenges with your application, we can help Recently, we published our new decorative coatings in rose/ you assess your coating process on a very similar machine,” says lavender colour, created with HiPIMS technology. Now the new Huub. “That reproduces your original circumstances as best as R&D system is operational, the Hauzer engineers are getting possible. If you have any questions or ideas that you’d like us ready to test various new target compositions. “We’re going to to work on for you, we invite you to get in touch! The new R&D try some really exotic mixes of elements!” says Chinmay Trivedi, machine will start running customer tests and development Process Technology Manager. “We can’t wait to get started on projects as of January 2024, and people are already getting in these new target compositions.” line.” The testing plan will of course include traditional technologies Check out a video clip of a new coating under development, with new target materials and less traditional technologies with with water-repellent properties: traditional target materials. But the team is most excited for trying the new materials with the newer technologies, since that is an area never before explored. Are you interested in seeing what the Flexicoat 1500 can do for you? Contact Huub Vercoulen for more information at +31 77 355 9763 or HVercoulen@hauzer.nl.
Energy-saving upgrades for Hauzer and Bernex machines In a world increasingly focused on sustainability, energy efficiency and cost reduction, businesses are actively looking for ways to minimise energy consumption without compromising productivity. Hauzer and Bernex both developed innovative energy- saving features and upgrades for our existing machines, aiming to help you improve your operations and save on energy costs. Hauzer: energy-saving developments Hauzer Smart Fan From the Hauzer side, we offer the Hauzer Energy Saver and the By default, the fans that keep the cabinet (which houses the Hauzer Smart Fan, small-scale machine improvements with a power electronics) cool run constantly when the machine is great return on investment. on. However, there’s a safe temperature range. With a small adaptation, the fans can be programmed to run only when the Hauzer Energy Saver temperature in the cabinet nears the top of the safe range. Most Hauzer machines in the field are batch machines. This requires a minor electrical modification, which can be done The majority of them are not running 24/7. Albert Hendriks, by Hauzer technicians or your own, to save around 1.5 kWh when Sales Manager: “To prevent needless energy use, we developed the fans are not running. a software functionality with auto-shutdown after a period of idleness. This can save around 15 kWh per machine in energy save Of course, the latest generation of water-cooled power supplies mode, compared to normal pumping or standby mode. The best and electronics provide a higher efficiency than old power thing about this feature is that it’s easy to implement – it can be supplies. For companies considering purchase of a new machine deployed fully remotely on most machines. The latest machines or bigger upgrade, that may be a plus. can even do more complex scheduling for the auto-shutdown.” In addition, there are site-specific options. Albert: “We have had success in energy saving with smart use and routing of cooling water, for instance. If you’re interested in solutions like that, please get in touch! We would be happy to take a look with you.” Would you like to know more about Hauzer upgrades? Please contact Albert Hendriks, Sales Manager at +31 77 355 97 11 or AHendriks@hauzer.nl. 24
Bernex: new ROB furnace upgrade In contrast to Hauzer’s energy savers, which are easy to implement, Bernex offers a large upgrade: a completely new furnace design. In addition to significant energy savings, the new furnace also improves temperature stability, coating homogeneity, machine productivity, component lifetime and ease of maintenance. The main energy saving contribution comes from the reduction in heat-up time by about an hour. The power use while heating up the machine remains the same, but over 40% less time. This was achieved by replacing the heating coils with meander- type heating elements. These elements give better control of the temperature as well, which results in better uniformity of the coating. Other benefits: Reduced heat-up time allows for more productivity 300% more lifetime expectancy of the furnace Low downtime due to broken heating elements, which can be replaced without disassembly of the furnace The new, more productive and more sustainable furnace design is standard on new Bernex machines but also available as upgrade for existing Bernex CVD systems. OLD SYSTEM NEW SYSTEM Would you like to know more about Bernex upgrades? Please contact Reto Moor, Project Manager After Sales at +41 62 287 86 53 or Reto.Moor@ihi-bernex.com. 25
CVI coating technology for fibre-reinforced composite materials In the last Hauzer for You, we introduced the Bernex Fibre Coater, a technology for continuous coating for fibre tows. This technology is used for protective coatings on fibres (500 to >2000) either in a tow or a preform. These fibres can be ceramic or graphite, are usually several micrometres in diameter, and are used in the manufacturing of composite materials. Today, Bernex Head of Technology Hristo Strakov shares new applications and the latest test results for the Pyrolytic Carbon (PyC), Boron Nitride (BN) and Silicon Carbide (SiC) coatings. Improving the material properties of composite of the Fibre Coater. Coatings like Boron Nitride (BN), Silicon materials with coatings Carbide (SiC) and Pyrolytic Carbon (PyC) and their combinations The advantage of fibre-reinforced composite materials with a in form of multilayers are widely used for manufacturing of metallic (MMC) or ceramic (CMC) matrix is that they can combine different composite materials. the optimal properties of different materials. Using coated fibres in such a matrix allows composite materials to be used The unique qualities of CVI coatings in conditions where other materials usually fail. Applications The high quality of the PyC, BN and SiC coatings comes from are wide-ranging: for instance, anywhere there is a need for the finesse and tuning that the Bernex team has been able materials that are stable and strong at high temperatures, such to do. “With CVI processes, the goal is to get a homogeneous, as in aerospace components. The interface between the fiber and defect-free coating on all the fibres in the tow or preform,” the matrix is important – thus the need for advanced coatings. explains Hristo. “With our process tailoring, we can control the stoichiometry and crystallinity of the coating to give the coating For addressing the current market needs, an efficient technology properties that best match our customer’s requirements. is required that can produce the necessary quality at lower costs. For instance, we can go beyond a crystalline structure for BN and A continuous coating system, which can also produce coatings at have a rather wide stoichiometry capability for SiC. Infiltration high growth rates, is the key to success. Hence the development rate is the critical metric for good homogeneity, and we achieved a wide, robust process window for a good homogeneity.” 26 Hauzer for You No. 40
Test results from the Bernex R&D department Test results from the Bernex R&D department The first example below shows a Pyrolytic Carbon coating, The next example shows a scanning electron microscopy (SEM) deposited at a constant temperature of 1150°C, different image of a homogenous SiC coating, as it can be seen on the fiber. chemical concentrations and gas resistance times. The coating In this case, this is an Si-rich coating composition tailored towards is very homogeneous and defect-free, with clearly detected D- a specific application. The Raman spectrum below confirms the and G-bands, and a coating thickness of about 180 nm. With this SiC and also the Si content. Such coatings can also be produced coating process window, outstanding infiltration coefficients of in wide process parameter windows, such as temperatures 0.9 to 1 can be achieved, which means fibres on the inside of between 1000 and 1150°C or process pressures in the range of 10 the tow can reach the same coating thickness as fibres on the to 20 mbar. This process parameter window produces very good outside. homogeneity and extremely good infiltration coefficients of around 1, which means an equal coating thickness in the center and at the edge of the fibre tow. Raman spectrum and scanning electron microscopy image of Raman spectrum and scanning electron microscopy image of PyC-coated fibres. SiC-coated fibres. The final example proves the production of a homogeneous, defect-free BN coating at temperatures above 850°C and process pressure in the range of 1 mbar. This example, with a thickness of 190 nm, shows a crystalline coating with a clearly visible hexagonal structure and 002 peak at 26° (2Theta). In this operation window, a good homogeneity was achieved, with infiltration coefficients of 0.8 to 1.1. XRD spectrum of BN-coated fibres Would you like to learn more about the test results and new applications of the Bernex CVI coatings? Please contact Hristo Strakov at +41 62 287 86 64 or Hristo.Strakov@ihi-bernex.com. 27
Dornbracht: Elevating design with unparalleled finishes In a world where more and more companies attempt to create unique designs, few brands master the art of beauty quite like Dornbracht. This German powerhouse sets the standard in design, functionality and quality for fittings and accessories for bathroom, spa, and kitchen. Their carefully crafted fixtures provide timeless sophistication, mirroring the brand’s motto: Leading Designs for Architecture. Hauzer is proud to count Dornbracht among our customers, having delivered one physical vapour deposition (PVD) system to them and working on a second. 28 Hauzer for You No. 40
Global vision, local craftsmanship Headquartered in Iserlohn, Germany, Dornbracht operates in more than 125 markets worldwide. Despite their expansive reach, the essence of their craftsmanship is local. “Our tap designs, some of which are celebrating their 30th birthdays, are more modern than ever,” says Benedikt van Vliet, New Business and Program Manager. He is establishing the PVD line in the company and is an expert in this coating technology. “We aspire to create designs that last for generations.” Dornbracht is not just riding the wave of the changing consumer landscape; they are actively shaping it. “We’re seeing greater demand for specialised finishes – those that offer a tactile experience or allow consumers to personalise their interiors,” says Benedikt. Chrome, long the staple of bathroom fittings, is now sharing the limelight with rich gold finishes and dark surfaces. Investing in the highest technology standards The Dornbracht quality can only be achieved by expertise in their chosen technologies. “Our expertise in electroplating, for instance, goes back many years,” says Benedikt. “Globally, we are among the leading companies in this field. However, future trends are moving beyond the colours that can be achieved by plating. With PVD technology, we are looking to add new colours to our portfolio. Because PVD coatings are so thin, they can be used over our unique brushed surfaces without changing them.” Searching for a long-term technology partner To find the right supplier for PVD equipment, Dornbracht did comprehensive market analysis and rigorous tests. “Hauzer fits our criteria best, from speed in low-temperature processes to intricate decorative coatings,” Benedikt explains. “We work a lot with plated surfaces, brushed parts, and complex product geometries, and any technology we selected needed to be able to handle all that.” After that rigorous selection process, Dornbracht ordered a fully turnkey system from Hauzer, including cleaning line. “We wanted all our technology to come from one party,” says Benedikt. “Now, we have a single contact person who can communicate with us in our native language, which keeps barriers to contact low.” A partnership rooted in innovation The relationship between Dornbracht and Hauzer is more than just a transactional one; it’s a collaborative quest for innovation. Dornbracht is redefining surface design with their new PVD capability, which will complement the company’s electroplating workshop. Hauzer is pledged to support that challenge with a 5-year service and maintenance contract, during which we provide all service and maintenance of the machines and cleaning line. During this time, Hauzer and Dornbracht will also collaborate intensely on coating development; a relationship that both parties hope will last for decades. “Currently, we are getting to know our first Hauzer machine,” says Benedikt, “building our in-house proficiency and expertise. Then, we will introduce our own colour palettes that deviate from market standards, further solidifying our reputation for unique designs and high-quality finishes. We’ll be looking at new materials, gases, and reacting partners, essentially rethinking the coating process with Hauzer by our side.” There is no substitute for excellence “We always aim for unique designs and outstanding quality, and we’ve found a partner in Hauzer,” Benedikt concludes. “We are not merely reacting to market trends; we are setting them.” The partnership between Dornbracht and Hauzer promises to deliver not just quality and functionality but also Copyright: Dornbracht new, unique finishes to elevate the bathroom and kitchen into living spaces. 29
Other plasma processes on Hauzer machines: plasma cleaning, etching, and nitriding The multifunctional power of plasma Plasma is often called the fourth state of matter, in addition FIR (Focused-Ion Rapid) etching is a variation on plasma etching, to solids, liquids and gases. Plasma is created when an energy which is known for its tunability. With a standard plasma source, source, like an electric current, is applied to a gas, liberating the etching rates may vary based on the position in the chamber. electrons from atoms and creating a mixture of ionized atoms, With FIR etching, you can specify etching times for various free electrons, and neutral atoms. In the world of surface positions, resulting in a more uniform etching result. Moreover, treatment, plasma opens the door to a variety of advanced, FIR etching is generally faster. tunable processes. Plasma cleaning and etching for better coating adhesion Surface preparation is essential for ensuring strong adhesion of a PVD coating. Plasma cleaning and plasma etching both play a role in this. Philipp Immich, Director of Process Engineering, says, “They are both pre-treatment steps, but with different purposes. Plasma cleaning is used as a kind of chemical etching to remove organic residues, and plasma etching removes the oxide layer on the substrate.” Plasma cleaning uses hydrogen gas for the plasma. Hydrogen plasma is chemically reactive, so it can remove organic contaminants (which mostly consist of carbon-based molecules) by transforming them into CO2, H2O and other innocuous molecules. Plasma etching uses argon gas for its plasma. Argon has a heavier weight than hydrogen. The argon ions are ideal for physical bombardment, stripping away the oxide layer that often forms on surfaces from metallic substrates. 30 Hauzer for You No. 40
Plasma nitriding: a better support structure for your coating Philipp: “The easiest way to picture it is this. Think of a pane of Unlike cleaning and etching, which focus on removing materials glass; that’s your PVD coating. If you put your PVD coating on a from a surface, nitriding aims to add something – namely, soft substrate material, that’s like putting a pane of glass on a nitrogen. By applying plasma to nitrogen gas, the stable N2 bed. It protects against scratches and wear, but the glass breaks molecules are broken down into atomic nitrogen. These atoms easily. Nitriding increases the surface hardness of soft metallic easily diffuse into the surface of metallic objects, reacting with materials. Putting a PVD coating on a nitrided surface is like the metals present to form nitrides, like CrN or FeN. The result is putting the pane of glass on the floor: it’s just as thin, but now a much harder, wear-resistant surface, which provides a better you can easily walk on it.” support for the PVD coating you put on top. The combination process of plasma nitriding directly followed by a PVD coating Gas nitriding is an old, established technology. The benefit of is called a duplex process. Our Nitrocoat duplex coatings are using plasma is that you can use the benign N2 gas as a precursor. especially suited for forming, high-pressure die casting and This avoids the need for hazardous materials like ammonia, and forging tools to significantly extend the lifetime of the tool. reduces the safety measures needed. For plasma nitriding, the process temperature can also be lower than for conventional nitriding, saving energy. Typical plasma nitriding temperatures are in the range of 380-500°C, depending on base material and the process time. By adjusting different process parameters (e.g. process temperature, gas composition, pulse length and pulse frequency) it is possible to tune the process to avoid the growth of a compound layer or white layer, which commonly forms on the surface. For later PVD coatings, a diffusion zone without compound layer is preferable. By adding C2H2 gas during the plasma process, plasma carbonitriding becomes possible, providing toughness benefits in certain applications. Images: CrN on untreated tool steel substrate after impact tests. Plasma treatments in your Hauzer machine Hauzer machines can perform plasma cleaning, etching and nitriding and PVD coating on a batch of components and tools without having to break the vacuum in between the different processes. This is not just convenient; it’s also a significant energy saver. Heating is one of the most energy-consuming phases of these processes, and having these functions in one machine eliminates additional heat-up and cooling cycles. In addition, because there is no need for moving the products from treatment to treatment, there is no chance of new oxidation or contamination occurring before the coating step. Images: CrN on plasma nitrided tool steel substrate after impact tests. In summary, from ensuring microscopic-level cleanliness to modifying surface properties, plasma processes are key to high- performance coatings. Are you interested in learning more about the benefits of doing these processes on a Hauzer machine? Contact Philipp Immich at +31 77 355 97 80 or PImmich@hauzer.nl. 31
Albrecht + Schumacher Oberflächentechnik GmbH: Success built on expertise For this edition of Hauzer for You, we spoke to Peter Albrecht and his son, Mario, about their coating service company Albrecht + Schumacher. Founded in 1996, Albrecht + Schumacher has grown into a formidable player in the German industry with a team of 25 professionals. Peter Albrecht and Johann Schumacher started the company with a physical vapour deposition (PVD) machine they built themselves. Today, the company serves a diverse range of industries with their seven coating machines – including a Hauzer machine with HiPIMS technology. 32 Hauzer for You No. 40
High-service company in the North of Germany Albrecht + Schumacher offers a comprehensive array of services. What sets them apart is their end-to-end solutions, including in-house polishing. “We’re broadly oriented, and capable of quick and reliable turnarounds,” says Mario, one of the second-generation leaders prepping to take the helm. “In addition, we have our own delivery service to facilitate local customers.” “The first machine we had was a home-built arc machine with five targets,” says Peter. “Our portfolio grew with arc, sputter and PACVD machines, and now we also have HiPIMS capability.” The company now boasts a 2000m2 plant, including workshop and office. Their customer range expanded similarly over time. Albrecht + Schumacher started with coatings for cutting tools, but now also serve industries like the plastic and extrusion industry, metal machining, forming and moulding, and machine parts. Continuous investment in technology Among Albrecht + Schumacher’s numerous growth investments is their recent acquisition of a Hauzer Flexicoat 850 machine with HiPIMS technology. “We wanted a machine that we could configure ourselves, for maximum flexibility,” Mario Albrecht explains. “Hauzer provided just that. They’re a partner that’s reliable, fast, uncomplicated, and open. We also appreciate the excellent service level, especially remote troubleshooting. The machine is incredibly maintenance-friendly and is easy for frequent technology shifts, which is key for our diverse clientele.” Albrecht + Schumacher also develop customer-specific coatings, which are often made to customer specifications and then enter the general portfolio. Changes are coming at Albrecht + Schumacher What’s next for Albrecht + Schumacher? A seamless generational transition is in the works. Both Mario Albrecht and Timo Schumacher are gearing up to take over their fathers’ respective roles. “In the long run, we want to replace all old coating technology with new tech,” says Mario. “Flexibility is our motto.” Both sons bring a blend of experience and academic backgrounds that will help them understand and meet customer needs, and take the company into the next decades. With a commitment to quality, a flair for innovation, and a solid plan for the future, Albrecht + Schumacher shows what expertise and ambition can achieve. As the firm continues to serve their wide range of market, their central philosophy remains unchanged: stay flexible, stay reliable, and most importantly, stay customer-focused. 33
First Hauzer Flexliner systems sold for hydrogen technology Hydrogen has the potential to claim central stage as the fuel of the future, a game-changer in the quest for sustainability and energy independence. At Hauzer, we are at the forefront of this technological revolution, developing the high-quality coatings and high-throughput coating technologies needed to deliver the necessary production volumes to make hydrogen fuel cells and electrolysers a commercial success. With our H2 Product Team, we recently marked a significant achievement: the sale of the first few Hauzer Flexliner systems to global manufacturers of fuel cells. This underscores our strong position in the industry and validates the direction Hauzer has chosen. The future of hydrogen technology Hydrogen technology looks to have a bright future. It could play a crucial role in reducing greenhouse gas emissions. In fuel cells, hydrogen produces only water as a byproduct. In itself, hydrogen is also an effective energy storage medium, which is easier to store and transport than for instance electricity in batteries. It can be used for many different applications, from fueling vehicles to power generation for stationary applications. In addition, hydrogen is an important feedstock material for a range of industrial processes that currently use 34 Hauzer for You No. 40 39
Promising fuel cell technology Fraunhofer IST: championing a holistic Proton exchange membrane (PEM) fuel cells view of industrial improvement are a promising technology for a broad range of Christoph Herrmann, Director of the vehicles, allowing fast, efficient conversion of Fraunhofer Institute for Surface Engineering hydrogen into electricity. Why are these fuel cells and Thin Films (IST), also sees a vital role for so interesting? hydrogen for industrial decarbonisation. “We High efficiency. The 60% efficiency in converting are working with many large European players hydrogen into electricity is suitable for commercial to develop real-life hydrogen applications,” he vehicles. says. “One part of that is our highly automated Clean and eco-friendly. No polluting byproducts. fuel cell stack production line, where we Quick start-up. Quick response time for start-and- investigate fuel cells from component to stack stop traffic. level and from production to end of life. The Quick refueling, high range. Refueling hydrogen can coatings for bipolar plates play a significant be as fast as refueling petrol. role in our research, and we are testing them in Versatile. PEM fuel cells can function under a wide terms of efficiency gains, lifetime, and more. A range of operating conditions. broader role for coatings can be found in other Costs. The cost of PEM fuel cells has been decreasing components in the hydrogen infrastructure: over the years and is expected to fall even more. valves, joints, electrolysers… many of these petroleum-based feedstoc include parts that need to be coated to protect Hauzer’s role in coating solutions and them from the influence of hydrogen. technology At Hauzer, we are working relentlessly on creating ”What sets Fraunhofer IST apart is its dedication cost-effective, efficient coating solutions. We are to holistic understanding and lifecycle thinking. in the sampling and approval phase for several “When it comes to any improvement that international companies. The need for electrolysis is rolled out on an industrial scale,” says solutions, especially, is high, we are working on Christoph, “it is important to quantify the finding the right coating for these applications. impacts. For instance, electrolyser coatings Current state-of-the-art coatings use precious with precious metals, or an alternative. Is it metals like platinum or gold. Developing a coating strictly better? In terms of cost, energy use, that can provide the right characteristics without supply risk, environmental impact, circularity using these expensive materials will be a tremendous and product lifetime? If we move to alternative breakthrough for cost reduction. Hauzer is currently materials or technologies, no disadvantages launching a dedicated PVD platform to coat metallic are allowed. It is our desire as Fraunhofer IST to bipolar plates used in PEM electrolysers, based on deepen these discussions.” the Flexliner® family of inline coating equipment. Fraunhofer IST: championing a holistic view of industrial improvement Christoph Herrmann, Director of the Fraunhofer Are you interested in working with Hauzer to further develop your fuel cell or electrolyser concept? For more information on Hauzer Flexliner systems or hydrogen solutions, please contact Thorsten Karla, Sales Manager New 35 Business at +31 77 355 97 59 or TKarla@hauzer.nl.
Focus on customer satisfaction: introducing permanent helpdesk support for Hauzer and Bernex In recent editions of Hauzer for You, we have been keeping you up to date with the continued developments of the Hauzer Customer Service and Care (CSC) department. This shows our unwavering commitment to improving customer and partner satisfaction worldwide. We highlighted initiatives like improved service modules, quicker spare parts availability, and faster delivery times, all geared to maximise uptime. In this Hauzer for You, we are thrilled to share the latest addition: our permanent support helpdesk. If you are interested in in-depth details of our service modules Please contact your account manager to receive the brochure or check our downloads section 36 Hauzer for You No. 40
Permanent helpdesk support from Venlo and Olten Richard Poelen, Director of Global CSC, introduces the new helpdesk: “We’re proud to roll out our permanent support centers in Venlo for PVD and Olten for CVD. This new development means immediate, professional technical expertise is just a phone call away. When you’re facing malfunctions or need troubleshooting, our helpdesk team can dive deep into technical issues, offering both first and second-line support. The goal? To minimize downtime and get your systems back online as quickly as possible.” The helpdesk engineers can also escalate tickets up to the engineering department, for the highest level of technical expertise available. Customers who opted for the support module will enjoy prioritised ticket resolution and faster response times. Customers without a service contract will still receive help with the same level of expertise, on a fee-for-service basis. Direct contacts for technical assistance While your account manager remains your go-to for commercial inquiries, our newly established helpdesks are now your direct line for all technical matters. This two-pronged approach ensures that, whether you have a sales question or a technical one, you will have the support you need. The helpdesks operate on European time, so it may be faster to contact your local branch office first if you are located in Asia, Oceania or North America. They will be able to help you with commercial and technical support in a more convenient time zone. Our local Hauzer branch offices are in close contact with our helpdesks in Venlo and Olten. Helpdesk contact information Helpdesk Hauzer Venlo Helpdesk Bernex Olten helpdesk@hauzer.nl support@ihi-bernex.com +3177-2072727 +4162 2878580 For the helpdesk opening hours, please check our website. Introducing the Customer Portal Richard has another development to share: “We’re in the early stages of developing a Customer Portal, a digital environment where you can monitor service tickets, request quotes, and much more.” To better help our customers, we will equip the portal with increasing functionality. The Hauzer Group Global Customer Service and Care department is continually investing in practical ways to make your experience with us smoother, more efficient, and ultimately more satisfying. Richard: “We believe that these new features, along with our established service modules, are pivotal steps in that direction.” 37
Better employee experience at Bernex with the competence matrix At Bernex, the HR department has been implementing improvements for more than two years now. Jana Rauch, Bernex Human Resources Manager, gives an update on one of the milestones within the HR developments: the competence matrix. “With this matrix,” Jana says, “we want to strengthen our employee experience. It can help us precisely classify each employee and promote their further development. We’re integrating the competence matrix with the employee questionnaire next January. This will give us an overall picture of our employees, and we will know exactly how to most effectively apply our budget to strengthen our employees and our company. We are also streamlining the tools to broadcast new job openings, and expect that the synergies in this system will inspire existing and new employees for their growth at Bernex.” By using the matrix, Bernex have already been able to expand the teams in the areas of Customer Support & Care, the Software and Mechanical department and the Finance department with new employees. 38 Hauzer for You No. 40
New leadership: IHI Bernex welcomes Olivier Coddet as Managing Director IHI Bernex is ushering in a new era with the appointment of Olivier Coddet as Managing Director. Taking over from Michael Auger, Olivier intends to use this change in management as an opportunity to set new goals for Bernex’s continued growth within the Hauzer Group. A strong fit for Bernex Two years ago, recognizing the need for a fresh perspective, Olivier Coddet brings a rich background in materials science Michael began looking for new leadership. Olivier’s experience to the table. He started his career in coating R&D in 2002, made him the perfect choice. Michael: “Olivier really understands pioneering new PVD technology and travelling extensively. what our customers are thinking about, which makes it easy to As of 2007, he focused on tailoring diamond-like carbon coatings help create the best solutions for them.” Olivier’s impression of to customer applications in various countries, including North Bernex was immediately positive. “Bernex is a stable organization America, Brazil, Europe, China, and Singapore. with a full order book and no immediate challenges, and I’m looking forward to exploring the possibilities.” Olivier’s rise to Production Manager for DLC and decorative coatings, and later Business Unit Management, showcases his Michael Auger is stepping into a new strategic role within the leadership qualities. He was instrumental in improving his unit’s Hauzer Group. As Chief Customer Officer (CCO), he aims to turnover and expanding the team, reinforcing knowledge sharing optimise existing strengths of the unified global Hauzer Group and improving daily operations. and foster new business development. A strategic handover for both Bernex and Hauzer Embracing the future Michael Auger’s nine-year tenure as CEO of Bernex has been “All of Bernex wishes Olivier a warm welcome,” says Michael. characterized by innovation and growth, spinning out Bernex “I, personally, am looking forward to seeing which opportunities from Ionbond and joining the Hauzer Group. Under his leadership, he will take and where he will lead Bernex. Olivier’s strong Bernex has expanded its product line and global footprint. international perspective, expertise in materials science and proven track record promise an exciting future.” 39
Employee spotlight Frits Plüss Bernex Electrician I have a long history with Bernex – I started here 30 years ago after working for a subcontractor. It’s a decision I have never regretted for a day! Since then, I have been working in the Bernex assembly team, building the individual and customer- specific electrical control cabinets, and wiring all the electrical components and parts. I like my varied and independent work in a small, motivated team. Moreover, Bernex offered me the opportunity to broaden my horizon, travel to foreign countries and get to know foreign cultures during assembly assignments. Bernex is a success story, an innovative company which, since its foundation in 1902, has developed from a truck manufacturer to one of the world’s most important manufacturers of CVD coating systems. It is wonderful to work for a company with a history like that. I look forward to continuing to play my part in the success of Bernex. Welcoming interns back at Hauzer Throughout the history of Hauzer, interns have always been welcome at Hauzer. However, the Covid-19 pandemic temporarily put a stop to that. “Now, we’re happy to welcome two new interns at Hauzer again,” says Petra Rouleaux-Vermeeren, Hauzer Human Resources Manager. “One intern will be working on stock optimisation at Customer Service & Care and the other intern will be working on a thermal model for cathodes at System Architecture. This is an investment in the future of society and also the future of the company: these students do great work for us and bring in new ideas, and some of them may return to us as employees after graduating. We’re looking forward to having our interns around and will be happy to develop more future internship projects!” Are you interested in doing an internship with Hauzer? Reach out to Petra at PVermeeren@Hauzer.nl or Celine at CHamers@hauzer.nl and we will look at options that fit your profile.
Claudia Alt Bernex Tim Thissen Purchasing Hauzer I always wanted to work in an international company, so my Field service engineer switch to Bernex in 2017 was a great opportunity. I have over 29 years of experiencing in purchasing, and was already familiar I started working at Hauzer this May, looking for a job where I could with machine building companies. work with complex, high-tech machines. I also wanted to travel more for work. At Hauzer, I can combine these two really well. My job in the Purchasing Department is exciting and varied, with As a field service engineer at Hauzer, I’m currently learning the many responsiblities. I mostly look for solutions with suppliers. machines and getting some experience. Once I build my expertise, I also collect offers, place orders, and check the confirmation I will go all over the world for Hauzer and work on the machines at and delivery of the goods. All to make sure that we get the right the customers’ sites: installation, modification and service work. products in at the right time. A wonderful thing about working at Bernex is that the atmosphere is so good, and that people give I have a background in electrical engineering and have spent each other a lot of space to work independently. most of my career working on interesting, complex machines. The working environment at Hauzer is really good. Whether it is for advice or just a chat, the people I’ve met at Hauzer were all a pleasure to talk to. Working with friendly people really does make the job a lot more fun. I really like the variation in our work. Every day can be something very different; working on electric, gas, pneumatic, water, software (PC & PLC), just to name a few. Sometimes troubleshooting, sometimes maintenance – anywhere in the world. 41
New website for Bernex! Bernex is excited to launch a new website at www.ihi-bernex.com. The goal: to make it even easier for customers and other interested readers to find what they are looking for. The new website not only showcases Bernex’ long history and world-leading expertise, but also addresses markets, solutions and services to understand which Bernex equipment is the best match for your application. Topics on the website Market Aerospace, cutting inserts, industrial components, and the forming and moulding sector – these sectors all have their different requirements and applications. Check out Bernex’ expertise in each. Products CVD, CVA, CVI and more – you will find out what these terms means and which technology is the right approach for you. Solutions Bernex has decades of experience when it comes to finding the right solution for a wide range of applications, whether you need a turnkey coating facility or a novel and proprietary specialist coating. Services Bernex focuses on long-term relationships with customers. Services, from support to spare parts to upgrades to coating development, are part of how the Bernex expertise can help you become successful. And more! Visit the website and see for yourself. 42 Hauzer Hauzerfor forYou YouNo. No.39 40
43
Meet us DMP Imtex 27 – 30 November 2023 19 – 23 January 2024 Shenzen, China Bangalore, India Booth: 4K31 IHI HAUZER TECHNO COATING B.V. FC Expo SVC Techcon 28 February – 01 March 2024 04 – 09 May 2024 Van Heemskerckweg 22, 5928 LL Venlo, The Netherlands Tokyo – Japan Chicago – USA T +31 77 355 97 77 info@hauzer.nl Booth: 908 hauzertechnocoating.com